Delivering a 5% Idle Time Reduction for a Multinational Motorcycle Manufacturer
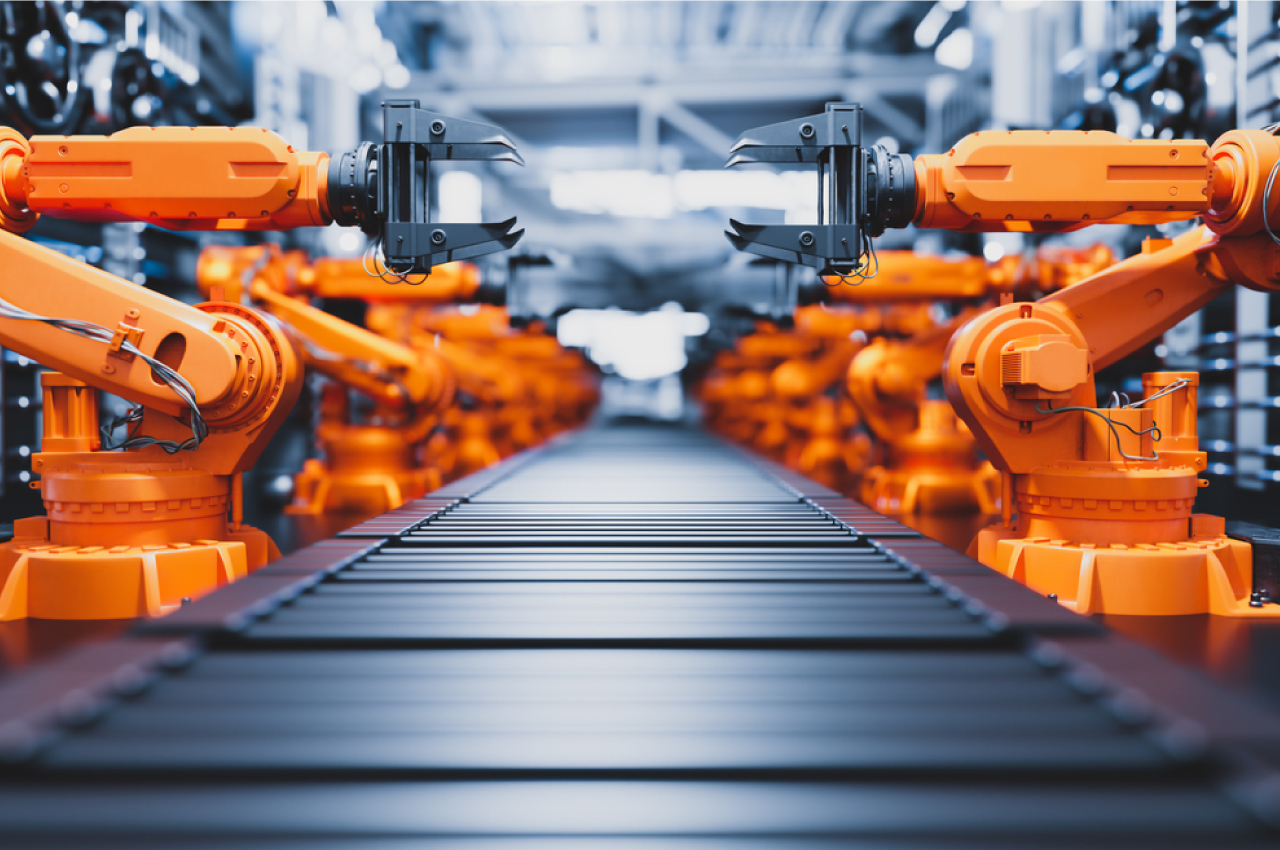
Impact Summary
• Optimised assembly lines with a 5% idle time reduction, elevating productivity and leading to an equivalent reduction in carbon emissions.
• Future-proofed capital expenditure (Capex) for a 5% capacity increase, ensuring efficiency and scalability.
Overview
Ecolibrium collaborated with a leading multinational motorcycle manufacturer in India to elevate operational efficiency at their state-of-the-art manufacturing facility in Hosur. The challenge involved enhancing operational visibility and generating actionable insights to boost Overall Equipment Effectiveness (OEE). Dive into our case study to witness how we optimised assembly line operations by identifying and reducing machine idle time and cycle time, leveraging the capabilities of our AI-powered decarbonisation platform, SmartSense.
Objectives
The client, a key player in India's automotive sector, faced operational hurdles at their manufacturing plant, characterised by infrastructure limitations with no visibility of key equipment performance.
Despite resolution attempts by the existing vendor, challenges persisted. Ecolibrium's primary task was to give the facility team a comprehensive single-pane view of their machinery performance, including idle time and cycle time. The goal was to utilise these insights for a process optimisation solution, minimising and benchmarking idle time and elevating production unit efficiency throughout the plant.
Upon initial assessment, an infrastructure upgrade was evident. Ecolibrium replaced the plant's inadequate data logger with SmartSense's advanced sensor technology and integrated systems, featuring data science capabilities for a detailed view of key equipment operations. This upgrade, crucial for Current Signature Analysis, enabled a precise examination of machinery performance, including idle time and cycle time, energy consumption, and production metrics. The strategic integration of these technologies formed the foundation of our approach, which was focused on boosting throughput, benchmarking and optimising machine idle time and cycle time while reducing carbon emissions, aligning with the plant's operational objectives.
Outcomes
In Q1 2023, the implementation of SmartSense marked a significant leap in the plant's data acquisition capabilities, offering a single-pane operations view on one dashboard. Analysing amperage data, SmartSense’s proprietary algorithms provided nuanced insights into machinery performance on two key assembly lines, focusing on optimising idle time and cycle time and enhancing operational efficiency.
SmartSense's advanced analytics uncovered a substantial 5% idle time on the assembly lines, indicative of energy inefficiency and suboptimal production. Precise differentiation between machinery states—active, idle, and off—allowed for targeted strategies, optimising manufacturing, conserving energy, and maximising throughput.
Beyond data collection, SmartSense's AI analysis of cycle time variations between identical machines on different lines provided actionable intelligence for process refinement. This insight prompted a reassessment of the existing plant capacity, resulting in capital expenditure savings while meeting production targets.
The project's impact was further highlighted by SmartSense detecting cycle time anomalies in the highest-performing machines, hinting at a significant production increase in subsequent phases. SmartSense's comprehensive data and insights have become integral to strategic planning, sparking discussions to extend its deployment across three plants, scaling its transformative benefits.
Summary
The successful integration of SmartSense at this multinational motorcycle manufacturing plant in India exemplifies Ecolibrium's prowess in delivering transformative operational efficiency solutions. Our strategic approach, centred on refining data acquisition and harnessing SmartSense's advanced AI-ML algorithms, yielded substantial Capex savings alongside a 5% reduction in machine idle time, promoting energy efficiency. This project illustrates our capacity to translate intricate industrial data into actionable insights, propelling workforce productivity and manufacturing efficiency.
The project's scope and impact not only achieved but exceeded client objectives. Precise identification of idle time and revelation of hidden operational inefficiencies empowered the client to significantly enhance throughput, realising a remarkable 5% reduction in carbon emissions. These accomplishments were attained without requiring extensive capital investment in plant expansion, showcasing the efficacy of data-driven decision-making in bolstering operational sustainability and cost-effectiveness.
Experience the transformative power of SmartSense in elevating manufacturing efficiency. Our success at the multinational motorcycle manufacturing plant in India, optimising operations, enhancing throughput, and reducing emissions, underscores the crucial role of AI-powered analytics in refining manufacturing processes.
Our commitment is to steer organisations toward increased operational productivity, strategic advancements, and holistic process optimisation. To explore how SmartSense can pinpoint and capitalise on improvement opportunities in your manufacturing operations, contact our team today to schedule a personalised demo and consultation. Unlock the potential for operational excellence with SmartSense.